
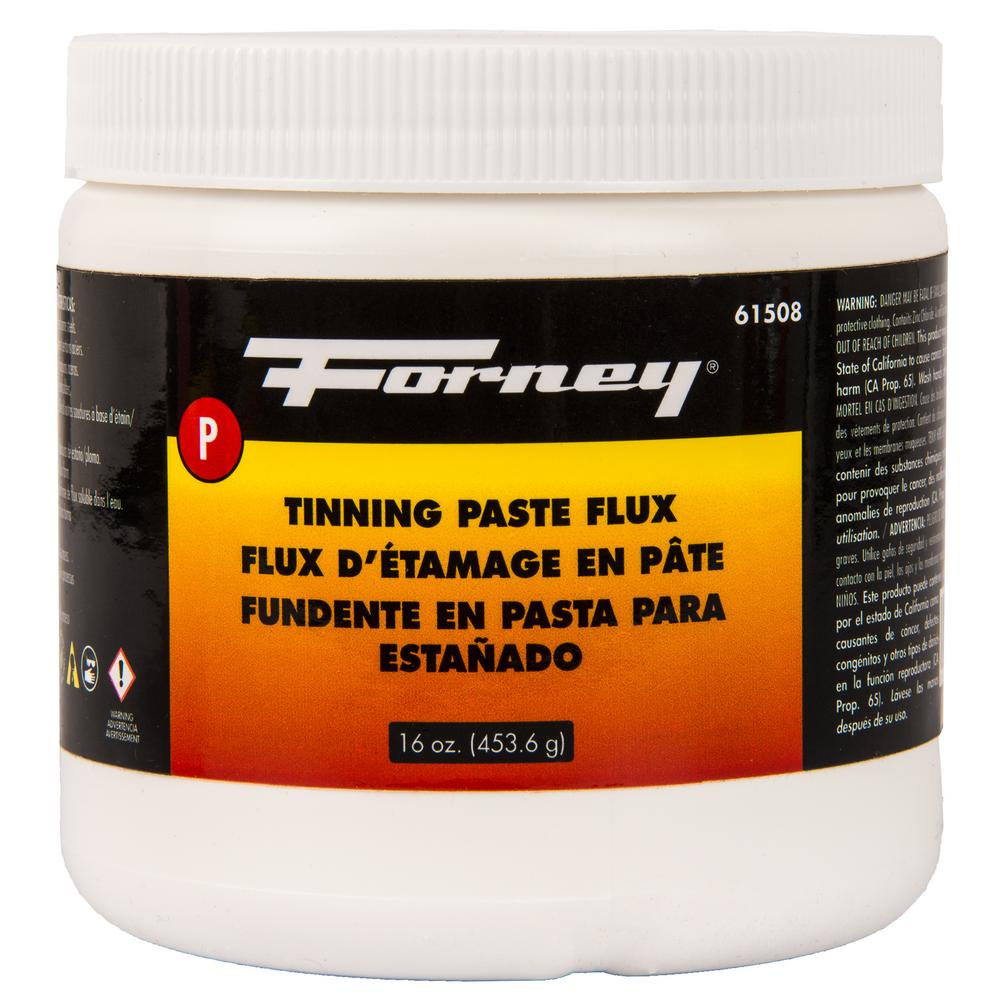
Mishandled or damaged shielding gas cylinder.Įither too low or too high welding current. Additionally, smaller gas molecules can blend with the weld metal, forming an impure compound. On the other hand, severe versions of porosity come in the form of blow holes or pits when large gas bubbles get trapped in the weld pool. Absence, lack, or too much shielding gas may lead to metal contamination, which reduces the strength of the weld. It is usually one of the common welding defects when using shielding gas, which is present in welding techniques such as TIG and stick welding. Porosity is the formation of holes in the weld pool resulting from gas bubbles that cannot escape. Selection of the correct welding materials.
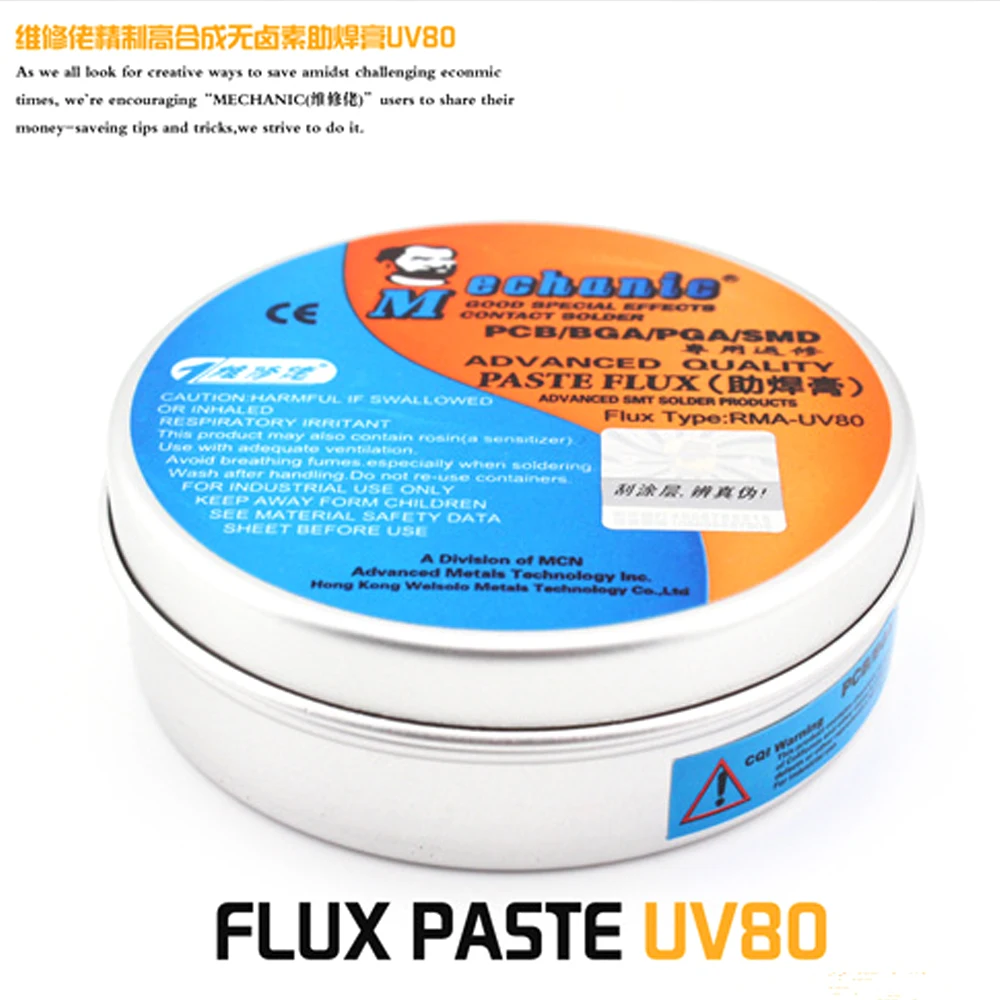
Preheating the metals and gradually cooling the weld joints. Use of high levels of sulphur and carbon. Rigid joints that constrain the expansion and contraction of the metal. Using hydrogen shielding gas in welding ferrous metals.ĭuctile base metal and the application of residual stress.
#TINNING FLUX FOR ELECTRICAL CRACK#
The weld crack may form hours or days after the metal’s cooling process.
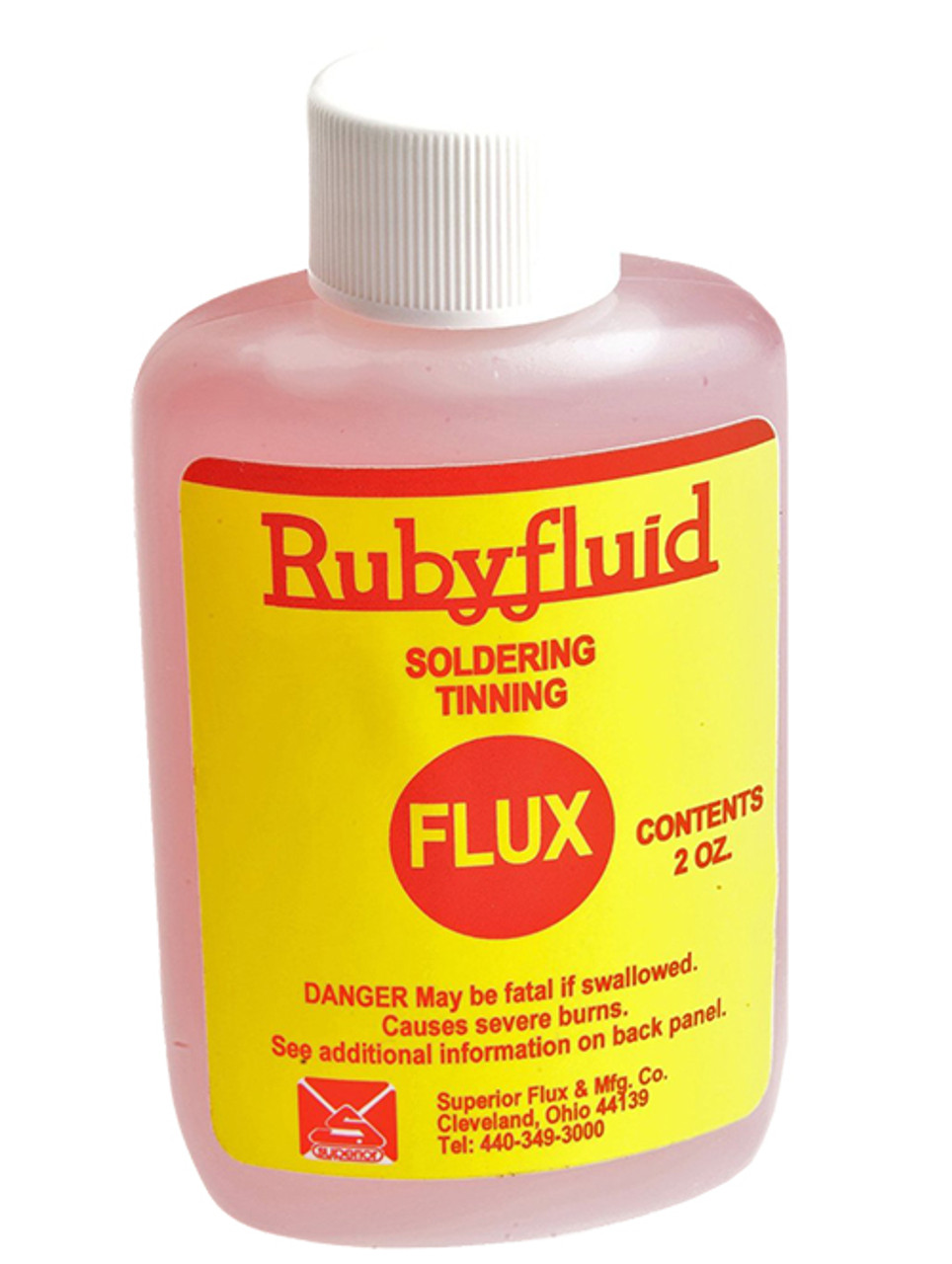
The primary reasons for hot cracks is when an incorrect filler metal is used and when the workpieces undergo high heating and cooling rates in processes such as laser welding.Ĭold cracks form after the cooling process of the weld metal. Hot cracks form when weld joints crystallise as the parent and base metals are heated above 10000☌. Welding cracks can also appear at varying temperatures: Crater cracks form at the end of the bead, where the arc concludes. Longitudinal cracks form parallel to the weld bead while transverse cracks form across the width. Weld cracks are mainly classified depending on how they form in the weld bead. CracksĬracks are the worst welding defect since they can rapidly progress to larger ones, which inevitably leads to failure. External Welding DefectsĮxternal welding defects refer to discontinuities in the weld metal that are noticeable to the naked eye. They can be classified into two major categories: internal welding defects and external welding defects. Weld irregularities occur for a variety of reasons and it results in different welding defects. In some cases, the metal can be repaired, but at other times the metal itself has melted and the welding procedure needs to be restarted. When a welded metal has a welding defect present, there are multiple options for resolving the issue. Common causes of welding defects come from incorrect welding patterns, material selection, skill, or machine settings, including welding speed, current, and voltage. They may also take place in the form of discontinuity or in material properties. Imperfections may arise dimensionally, wherein the result is not up to standard. It is defined as the point beyond the acceptable tolerance in the welding process. A weld defect results from a poor weld, weakening the joint.
